General working of PID controller
· When you step on the accelerator of your car, it moves slowly, then faster, and faster still, until you let off the accelerator.
· As you speed up, you will need to press the accelerator little less, then even less, until you reach the speed limit. As we have seen early unlike the digital world, where things are either “on” (1) or “off” (0), real processes have varying degrees of “on”.
· In this driving example, how much the accelerator is turned “on” depends on the car's current speed and how different the car's speed is from the speed limit.
· Controlling such a process with speed can be done with PID controllers.
Inside a PID Controller
What happens inside the PID controller ?
The below image is an schematic of the basic control
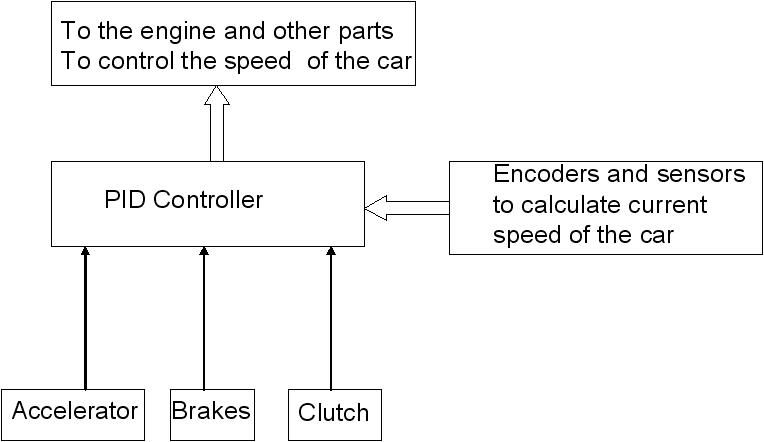
· Speed control is one fine example of a PID control loop. To calculate the output, it needs three factors.
· The first, (P), is the difference between the current speed and the desired speed (set points).
· The second, (I), is the sum of the differences over time. (The various speed values of the car in a running time)
· And, the third, (D), is the rate of change between sampled differences. (The time differences of each speed you reach)
· Each factor is scaled by a gain constant; they are referred to as Kp, Ki, and Kd. The value of these gain constants determines how responsive the output will be.
· If the Kp, Ki, and Kd values are too high, the output (car's speed) will exceed the set point (speed limit-60 Kmph).
· If the Kp, Ki, and Kd values are too low, the output may never reach the set point (speed limit- 40Kmph).
· So by controlling the P, I, D values we can control a range of output like 40-60Kmph.
This is just a theoretical example for the purpose of understanding the basics of PID controller. In real time for controlling action many factors and variables,parameters are calculated before controlling a particular process.